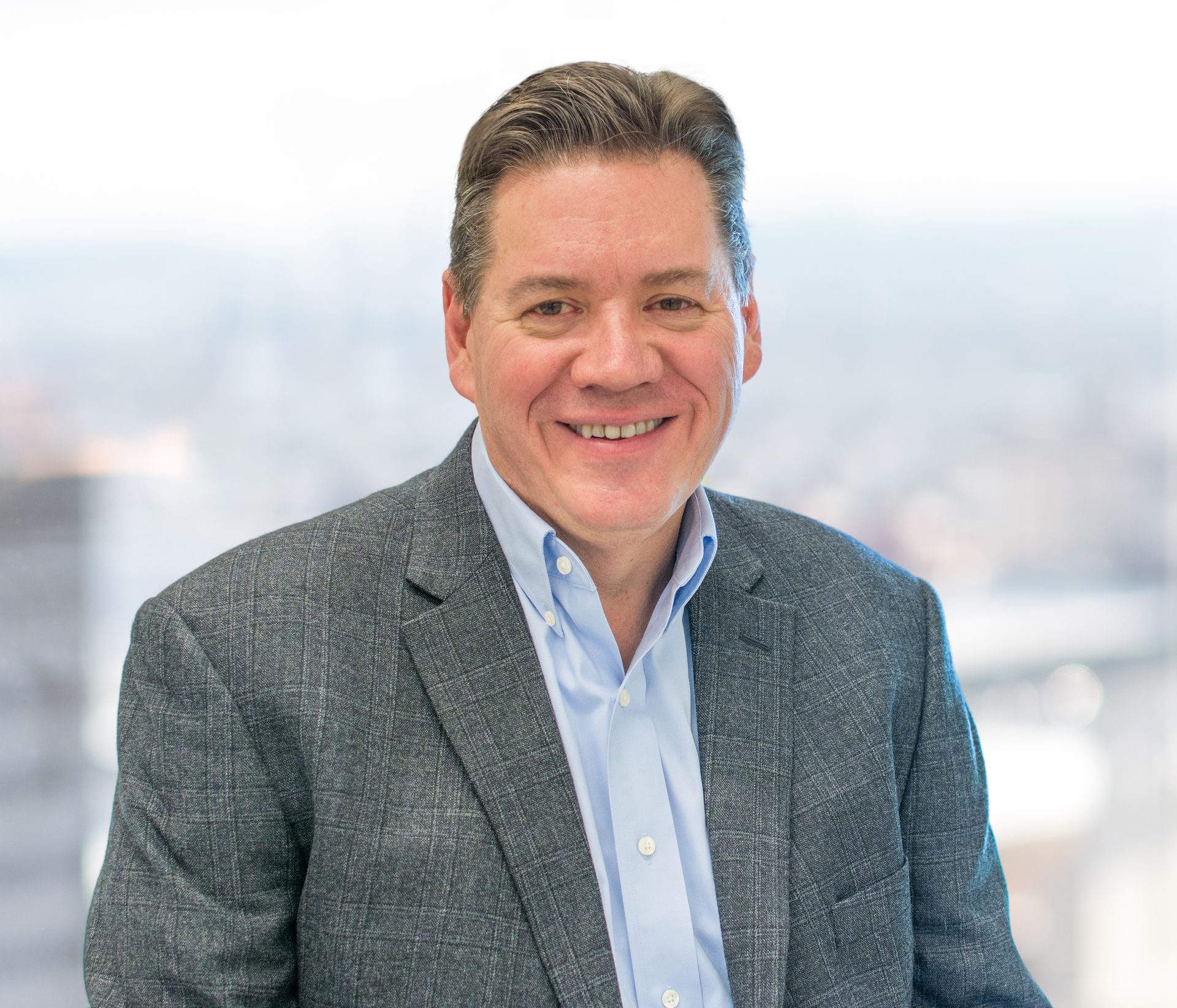
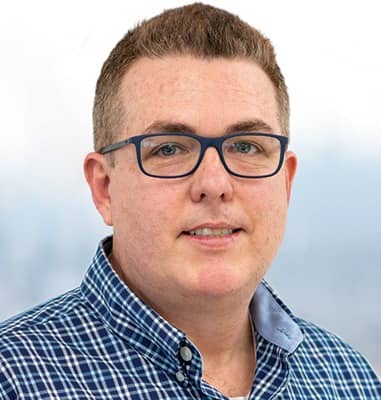
Balancing act
Understanding torque and rotating forces.
WATER COOLER CONVERSATION || By Ethan Grossman, P.E., CPD and Mark Jussaume
WATER COOLER CONVERSATIONS ||
By Ethan Grossman, P.E., CPD and Mark Jussaume
WATER COOLER CONVERSATIONS
|| By Ethan Grossman, P.E., CPD and Mark Jussaume
“Life is like riding a bicycle. To keep your balance you must keep moving.” — Albert Einstein.
Why does a bike stay balanced when you are moving and fall to the side when you are standing still? Anyone who has ridden a bike knows that if you keep moving you won’t fall but as soon as you come to a stop you will need to put your feet on the ground or risk tipping over. Most people think it has to do with the spinning wheels, like a gyroscope, that keeps the bike upright. It’s much more complicated than that, and not well understood by most engineers and scientists.
In 2011, an international team of bike enthusiasts reported that after 150 years of existence, no one could explain why a bike stays upright. They determined that to mathematically explain why a bike stays upright requires 25 variables including the angle of front forks with the road, wheel weight and wheel size.
Bikes seem so simple, and most of us would think we have a reasonable understanding of why they stay upright. The reason they stay vertical has very little to do with the spinning wheels and explaining how bikes stay balanced is much more complicated than explaining why planes fly. Even still, the curiosity in us is what sometimes can strike a spark of inspiration and learn about the mechanics of spinning wheels or the spinning planets in the universe itself.
I would be willing to bet that most of us have tried out a toy spinning top at some point in our childhood. Some of us may have even had one of those really cool gyroscopes that spun around on a stand and could do tricks with. It’s interesting to me what keeps a top spinning and how its axis of rotation starts to drift before it comes to rest. While we may not be able to explain how a bicycle stays balanced, we can start to understand the forces that work on spinning objects.
I’ll be the first to admit that I always thought torque was the force that was applied to the end of a lever, like a torque wrench. Distance times force was simple enough to understand. For example, 20 foot-pounds meant you applied 20 pounds of force to a wrench — or lever — that was 1 foot long. As it turns out, torque is the rotational equivalent of that linear force. The interesting part is that the direction of torque is along the axis of what is being turned. In the case of a nut being tightened or loosened, the torque acts in the direction of the bolt axis, depending on if you are doing “righty tighty or lefty loosey.”
The most common concern for building engineers when it comes to torque and rotating forces is how we specify our rotating equipment. We should think about what types of fans and pumps we specify; end-suction, horizontal split case, vertical, in-line, etc. and understand how the shafts and bearing lives are affected.
Understanding static concepts is fundamental to design and engineering. What happens when something starts to actually move is a different story, sometimes best understood by example or experimentation. In the example of the spinning top, torque and gravity counteract one another. As the angular velocity begins to decrease, you may notice that the axis starts to shift. This is called gyroscopic precession, or precession for short. Upon further observation, we can see that the precession increases as the top begins to slow down, as if the top had a life of its own, balancing the forces acting upon it to remain upright.
In the field of building engineering, there are few if any examples of gyroscopic precession. Like a bicycle, it is beneficial to fix the axis of rotation so that we can better control the forces in play and perform useful work. One example that does come to mind of a rotating mass and an applied force vector is that which is caused by the governor on a diesel engine designed to drive a fire pump. While the variable frequency drive for electric motors has become commonplace in the last two decades, mechanical engineers figured out a way to control the speed of a rotating machine that is designed to react to a variable load, like that of a fire pump, centuries ago. The device is called a centrifugal governor. In fact, the first centrifugal governors were used to lower or raise grinding stones driven by windmills during the process of milling. This went back to the 17th century.
While centrifugal governors do not exhibit gyroscopic precession, or torque for that matter, they do utilize centrifugal force to raise and lower a sleeve on a spindle and throttle the amount of fuel being fed to an engine, thus varying the engine’s speed. A centrifugal governor rotates at a speed proportional to the engine speed. It has two metal flyweights that are attached to linkages and rotate around a rod that moves up and down on a center post.
Imagine a fire pump curve. As the pump takes on more load and operates near full flow, the diesel engine driving the pump would slow down and not deliver adequate flow and pressure. The governor would also slow down, and the rotating flyweights would drop towards the spindle, thus raising a spring, opening the throttle and allowing more fuel to the engine, causing it to speed up. The opposite would happen under low flow. Under a reduced load, the engine speeds up, the flyweights spin out further, thus closing the throttle and causing the engine to slow down.
The most common concern for building engineers when it comes to torque and rotating forces is how we specify our rotating equipment. We should think about what types of fans and pumps we specify; end-suction, horizontal split case, vertical, in-line, etc. and understand how the shafts and bearing lives are affected. Just the other day I came to understand from a pump manufacturers representative that pumps are designed not only to compensate for the rotational forces, but for the forces caused by the fluids being pumped as well.
Staying open and curious about how things work is essential to our growth as professionals and tradespeople. Next time you are struggling to solve a challenging problem just remember, you don’t have to explain how to ride a bike to enjoy it; just keep moving and you will stay in balance.
mikkelwilliam/E+ via Getty Images.
Ethan Grossman, P.E., CPD, is the plumbing and fire protection discipline leader at Smith Group’s Boston office. He can be reached by email at ethan.grossman@smithgroup.com.
Mark Jussaume, PE, is a vice president and the Boston office director for SmithGroup. Jussaume’s focus is creating a supportive environment that invites people to learn, grow and thrive. He joined the previous firm nearly 30 years ago as a mechanical engineer with a passion for performing meaningful work. His steady rise through a variety of leadership roles culminated in him serving as that firm’s CEO until it was acquired and successfully integrated into SmithGroup in 2018.